Best Siding for Cold Climates: Stay Warm & Save
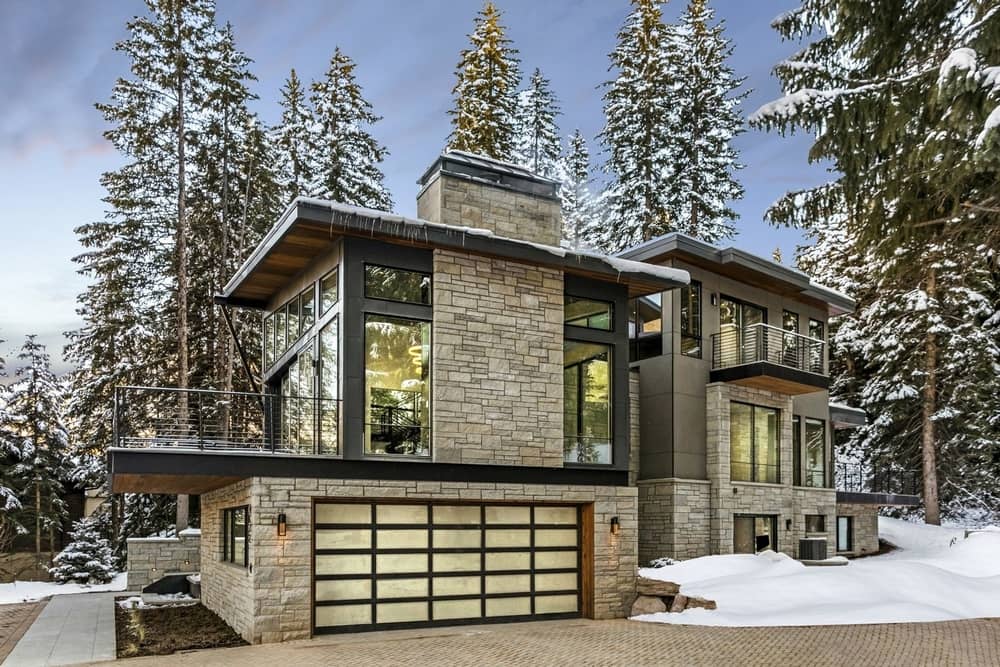
Best Siding for Cold Climates: Stay Warm and Save Energy—this crucial topic explores the vital role siding plays in maintaining comfortable indoor temperatures and reducing energy bills in frigid regions. Choosing the right siding isn’t merely an aesthetic decision; it’s a strategic investment in energy efficiency and long-term home protection. This guide delves into the characteristics of various siding materials, comparing their performance, cost-effectiveness, and maintenance requirements to help you make an informed choice for your home.
We’ll examine popular options such as vinyl, fiber cement, wood, and metal siding, highlighting their strengths and weaknesses in cold climates. Factors like insulation values (R-values), durability, resistance to moisture and ice damage, and overall lifespan will be key considerations. We’ll also provide practical advice on installation techniques, maintenance strategies, and cost comparisons to assist you in selecting the best siding solution for your specific needs and budget.
Introduction to Siding Materials for Cold Climates
Choosing the right siding for a cold climate is crucial for maintaining a comfortable indoor temperature and minimizing energy costs. Several factors influence the effectiveness of different siding materials in frigid conditions, impacting both thermal performance and longevity. Understanding these factors allows homeowners to make informed decisions that enhance both the aesthetic appeal and energy efficiency of their homes.
Selecting siding for cold weather involves careful consideration of several key aspects. Beyond the purely aesthetic considerations, factors such as insulation value (R-value), durability against moisture and extreme temperatures, maintenance requirements, and overall cost-effectiveness all play a significant role in determining the best choice for a particular home and climate. Ignoring these factors can lead to higher energy bills, premature siding failure, and increased maintenance needs.
Common Siding Materials for Cold Climates
Several materials are commonly used for siding in cold climates, each with its own advantages and disadvantages. Vinyl siding, while popular for its affordability and low maintenance, may not offer the same level of insulation as other options. Fiber cement siding provides excellent durability and fire resistance, but requires more maintenance than vinyl. Wood siding, a classic choice, offers aesthetic appeal but demands regular upkeep to prevent rot and damage from moisture and extreme temperatures. Finally, metal siding, such as aluminum or steel, provides exceptional durability and longevity, but can be susceptible to dents and requires careful consideration of thermal bridging. The optimal choice depends on a balance of these factors and individual homeowner priorities.
Factors Influencing Siding Selection in Cold Weather
The R-value, a measure of a material’s resistance to heat flow, is paramount in cold climates. Higher R-values indicate better insulation, leading to lower energy consumption. Beyond the R-value of the siding itself, the overall wall assembly’s insulation, including the sheathing and insulation batts, significantly impacts the home’s thermal performance. Therefore, choosing siding with a good R-value is only part of the equation; proper installation and overall wall insulation are equally crucial. Additionally, the material’s resistance to moisture is vital to prevent ice dams and water damage. Materials that effectively shed water and resist moisture penetration are crucial for preventing structural damage and maintaining energy efficiency. Finally, the long-term maintenance requirements and cost-effectiveness of each material should be carefully weighed against its initial cost.
The Importance of Insulation in Relation to Siding Selection
Siding’s role in a home’s thermal envelope is often misunderstood. While siding contributes to the overall insulation, its impact is secondary to the insulation within the wall cavity. The siding primarily acts as a protective barrier against the elements, preventing moisture intrusion and protecting the underlying insulation. A high-R-value siding material can improve insulation slightly, but the effectiveness of the overall wall system depends primarily on the quality and quantity of insulation installed within the wall. For instance, a home with insufficient wall insulation will experience significant heat loss regardless of the siding material used. Conversely, a well-insulated home with even a lower R-value siding will perform much better than a poorly insulated home with high R-value siding. Therefore, a comprehensive approach to insulation, encompassing both wall insulation and siding selection, is essential for optimal energy efficiency in cold climates.
Vinyl Siding in Cold Climates
Vinyl siding has become a popular choice for homeowners across North America, and its suitability in cold climates is a frequent topic of discussion. While it offers several advantages, understanding its limitations in freezing temperatures is crucial for making an informed decision. This section will explore the pros and cons of vinyl siding in cold weather, examining its durability, energy efficiency, and potential maintenance needs.
Vinyl siding’s popularity stems from its relatively low cost, ease of installation, and wide variety of colors and styles. However, its performance in extreme cold requires careful consideration.
Vinyl Siding Durability in Cold Climates
Vinyl siding’s durability in cold climates is largely dependent on its quality and proper installation. High-quality vinyl siding, often indicated by thicker gauge material and a higher impact resistance rating, is less susceptible to cracking or warping in freezing temperatures. Conversely, thinner, lower-quality vinyl siding can become brittle in the cold, increasing the risk of damage from impacts or thermal expansion and contraction. Proper installation, ensuring adequate ventilation behind the siding to prevent moisture buildup, is also paramount to its longevity. Improper installation can lead to issues such as expansion and contraction stresses causing cracking, or even moisture infiltration, which can lead to rot in underlying materials. Examples of such issues might include visible gaps between panels, or buckling in sections exposed to direct sun and cold.
Thermal Performance of Vinyl Siding
The thermal performance of vinyl siding varies depending on several factors, including the thickness of the siding itself, the presence of an insulating foam backing, and the overall wall construction. Thicker vinyl siding generally provides slightly better insulation than thinner siding. Some manufacturers offer vinyl siding with a foam backing, which significantly enhances its insulating properties. However, even with foam backing, the insulating value of vinyl siding is considerably less than that of other materials such as fiber cement or wood. For instance, a wall with standard vinyl siding may have an R-value of around R-4, while a similar wall with fiber cement siding might have an R-value closer to R-6 or higher, depending on the thickness and composition. The overall R-value of the wall assembly, including insulation within the wall cavity, is the critical factor determining energy efficiency.
Maintenance of Vinyl Siding in Freezing Temperatures
While vinyl siding requires relatively low maintenance, cold weather can present some unique challenges. Ice and snow accumulation can damage the siding if not properly removed. Aggressive scraping or the use of sharp tools can easily scratch or damage the vinyl surface. Furthermore, extreme temperature fluctuations can lead to the expansion and contraction of the siding, potentially causing minor cracking or loosening of panels over time. Regular inspection for damage and prompt repairs are crucial to prevent more significant problems. For example, a homeowner should regularly check for any loose or damaged panels, paying particular attention to areas exposed to direct sunlight or wind. Promptly addressing minor issues can prevent more extensive and costly repairs down the line.
Fiber Cement Siding for Cold Weather
Fiber cement siding offers a compelling alternative to vinyl and other materials in cold climates, boasting superior durability and energy efficiency. Its composition, a blend of cement, cellulose fibers, and other additives, results in a product that excels in resisting the harsh conditions often associated with freezing temperatures, snow, and ice.
Fiber cement siding’s longevity is a key advantage. Its inherent strength and resistance to rot, insect infestation, and fire make it a long-term investment that can significantly outlast vinyl siding. This translates to lower replacement costs over the lifetime of a home, a crucial factor to consider in areas with extreme weather. The material’s ability to withstand significant temperature fluctuations without cracking or warping contributes to its extended lifespan. The inherent density of fiber cement also makes it an excellent insulator, contributing to improved energy efficiency.
Cost-Effectiveness of Fiber Cement Siding
While the initial cost of fiber cement siding is typically higher than vinyl, its superior longevity and reduced maintenance needs often make it a more cost-effective choice in the long run. The reduced need for repairs and replacements offsets the higher upfront investment. Consider a scenario where vinyl siding requires replacement every 15-20 years due to damage from harsh weather, whereas fiber cement siding might last 50 years or more. The cumulative cost of multiple vinyl siding replacements can easily exceed the initial cost of fiber cement. Furthermore, the improved energy efficiency can lead to lower heating bills over the lifespan of the siding, further enhancing its cost-effectiveness.
Lifespan and Maintenance Comparison: Vinyl vs. Fiber Cement Siding
The following table compares the lifespan and maintenance requirements of vinyl and fiber cement siding:
Feature | Vinyl Siding | Fiber Cement Siding |
---|---|---|
Typical Lifespan | 15-20 years | 50+ years |
Maintenance Requirements | Regular cleaning; occasional repairs for damage | Occasional cleaning; minimal repairs; repainting every 10-15 years (depending on the paint type and climate) |
Susceptibility to Damage | Prone to cracking, warping, and fading in extreme temperatures | Highly resistant to cracking, warping, and fading; less susceptible to damage from impacts |
Cost | Lower initial cost | Higher initial cost |
Wood Siding in Cold Climates
Wood siding offers a classic and aesthetically pleasing option for homes, but its suitability in cold climates hinges on careful selection and maintenance. Certain wood types are more resistant to the harsh conditions of winter, while proper sealing and treatment are crucial for longevity and energy efficiency.
Choosing the right wood is paramount for enduring cold weather. The inherent properties of the wood, such as density and natural resistance to rot and insects, determine its ability to withstand freezing temperatures, snow, and ice.
Suitable Wood Types for Cold Climates
Cedar, redwood, and treated lumber are among the most suitable wood types for cold climates. Cedar and redwood are naturally resistant to rot and insect damage due to their high oil content, providing a degree of protection against moisture damage which is exacerbated in freezing conditions. Treated lumber undergoes a process that imbues it with preservatives, enhancing its durability and resistance to decay, making it a viable and often more affordable option. The treatment process significantly improves the wood’s ability to withstand the challenges of prolonged exposure to moisture and freezing temperatures. Choosing lumber graded for exterior use is also critical for ensuring sufficient strength and stability in harsh weather conditions.
Sealing and Treatment of Wood Siding in Cold Climates
Proper sealing and treatment are vital for protecting wood siding from the damaging effects of cold, snowy conditions. Water penetration is a major concern, as freezing and thawing cycles can cause expansion and contraction, leading to cracking and deterioration of the wood. A high-quality, water-repellent sealant applied before installation and periodically thereafter helps prevent moisture absorption. Regular inspection and prompt repair of any cracks or damage are also crucial to maintain the integrity of the siding and prevent further water damage. The sealant should be specifically designed for exterior use and should be reapplied every few years, depending on the product’s specifications and the severity of the climate.
Maintaining Wood Siding in Cold Climates
Proper maintenance extends the lifespan of wood siding and maintains its aesthetic appeal. Consistent attention to detail is key to preserving its value and energy efficiency.
- Regular Inspection: Conduct thorough inspections at least twice a year, in spring and fall, checking for any signs of damage, such as cracks, loose boards, or insect infestation.
- Cleaning: Gently clean the siding using a soft brush and a mild detergent solution to remove dirt, debris, and mildew. Avoid using high-pressure washers, which can damage the wood.
- Sealing and Repair: Promptly repair any damaged areas and reseal the siding as needed to prevent moisture penetration. This includes addressing any cracks or gaps that might allow water to seep into the wood.
- Snow Removal: Regularly remove heavy snow accumulation from the siding to prevent excessive weight and potential damage. Avoid using sharp tools that could scratch or damage the wood’s surface.
- Ice Management: Take precautions to prevent ice dams from forming, as these can cause significant damage to the siding and underlying structure. Proper attic ventilation is crucial for minimizing ice dam formation.
Metal Siding for Cold Climates
Metal siding offers a compelling option for homeowners in cold climates, providing a robust and energy-efficient exterior cladding solution. Its inherent durability and resistance to harsh weather conditions make it a long-lasting investment, while its reflective properties contribute to significant energy savings. This section will explore the advantages of metal siding in cold climates, comparing different types and outlining maintenance considerations.
Metal Siding: Durability and Weather Resistance
Metal siding’s exceptional durability stems from its inherent strength and resistance to damage from impact, rot, and insect infestation—common concerns with other siding materials. Unlike wood, it won’t warp, crack, or rot in the face of freezing temperatures, thawing cycles, and heavy snowfall. Its inherent weather resistance minimizes the need for frequent repairs and replacements, extending the lifespan of your home’s exterior and reducing long-term maintenance costs. The non-combustible nature of metal siding also offers an added layer of fire protection, a crucial consideration in any climate.
Comparison of Aluminum and Steel Siding
Two prominent metal siding options for cold climates are aluminum and steel. Aluminum siding is lightweight, relatively inexpensive, and corrosion-resistant due to its natural oxide layer. However, it can dent more easily than steel. Steel siding, while slightly more expensive, offers superior strength and durability, resisting dents and impacts more effectively. Galvanized steel, coated with zinc to prevent rust, is particularly well-suited to harsh winter conditions. The choice between aluminum and steel often depends on budget and desired level of impact resistance. For areas prone to hail or other high-impact weather events, steel is generally the preferred choice.
Appearance and Maintenance of Metal Siding
Metal siding is available in a wide array of colors, finishes, and styles, offering considerable aesthetic flexibility. Options range from smooth, painted surfaces mimicking the look of wood or other materials, to textured finishes designed to replicate the appearance of natural stone or wood shakes. Maintenance is generally minimal. Regular cleaning with water and a mild detergent can remove dirt and debris. While metal siding is highly resistant to corrosion, some types may require occasional touch-ups to maintain their appearance, especially in coastal areas exposed to salt spray. However, even with minimal maintenance, metal siding can retain its attractive appearance for many decades.
Energy Efficiency of Different Siding Materials
Choosing the right siding for a cold climate significantly impacts energy efficiency and heating costs. The thermal resistance, or R-value, of a siding material directly influences its ability to insulate your home and reduce heat loss. Higher R-values indicate better insulation. This section compares the energy efficiency of various siding materials commonly used in cold climates.
R-Values and Energy Consumption
The R-value represents a material’s resistance to heat flow. A higher R-value means less heat escapes in winter and less heat enters in summer. This translates to lower energy bills and a more comfortable living environment. While siding itself doesn’t provide the primary insulation for a home (that’s the responsibility of wall insulation), it contributes significantly to the overall thermal envelope and can reduce energy loss through the exterior walls. For example, a house with high-R-value siding might require less energy from its heating system to maintain a comfortable indoor temperature compared to a house with low-R-value siding.
Impact of Siding Materials on Heating Costs
The difference in R-values between various siding materials can lead to substantial variations in heating costs over time. Consider a home in a region with an average winter temperature of -10°C. A house clad in high-R-value fiber cement siding might experience significantly lower heating bills compared to a similar house with vinyl siding, which typically has a lower R-value. The savings can accumulate year after year, eventually offsetting the higher initial cost of the more energy-efficient siding. This cost savings is amplified in areas with extremely cold winters and long heating seasons.
Energy Efficiency Ratings of Siding Options
The following table summarizes the approximate R-values of common siding materials. It’s important to note that these values can vary based on the specific product, thickness, and installation method. These values represent a general comparison and should not be used for precise engineering calculations. Consult product specifications for exact R-values.
Siding Material | Approximate R-Value per inch | Energy Efficiency | Comments |
---|---|---|---|
Wood | 0.91 – 1.26 | Moderate | R-value varies greatly depending on wood type and thickness. |
Vinyl | 0.06 – 0.11 | Low | Primarily acts as a weather barrier, not a significant insulator. |
Fiber Cement | 0.11 – 0.15 | Low to Moderate | Slightly better insulation than vinyl but still relies heavily on wall insulation. |
Metal (Steel or Aluminum) | 0.00 – 0.05 | Very Low | Acts primarily as a weather barrier; requires significant wall insulation. |
Cost Comparison of Siding Options
Choosing the right siding for a cold climate involves careful consideration of both initial investment and long-term costs. While some materials offer upfront savings, others may prove more economical over the lifespan of your home due to lower maintenance needs and increased energy efficiency. This section provides a detailed breakdown to help you make an informed decision.
Initial costs vary significantly depending on material, labor costs in your region, and the complexity of your home’s exterior. Long-term costs encompass maintenance, repairs, and potential premature replacements. Factors such as climate exposure, quality of installation, and the homeowner’s maintenance practices also play a substantial role in the overall cost.
Initial Costs of Siding Materials
The initial cost of siding installation is influenced by several factors, including material cost per square foot, the size of the house, the complexity of the installation (e.g., multiple angles, intricate trim), and the labor rates in your geographic location. A general estimate for material costs per square foot (excluding labor and permits) might range from $2 to $15 depending on the material. Vinyl is typically the least expensive, followed by wood, fiber cement, and then metal, which tends to be the most costly. It’s crucial to obtain multiple quotes from reputable contractors in your area to get a realistic understanding of the total initial cost for your specific project.
Long-Term Maintenance Costs of Siding Materials
Long-term maintenance significantly impacts the overall cost of siding. Vinyl siding generally requires minimal maintenance, perhaps just occasional cleaning. Wood siding, however, demands regular painting or staining to prevent rot and insect damage, adding recurring costs. Fiber cement siding is relatively low-maintenance, but it may require occasional cleaning and repainting. Metal siding, while durable, might require occasional touch-ups for scratches or dents. These costs can add up over the years, potentially exceeding the initial cost difference between various siding types.
Twenty-Year Cost Comparison Chart
The following chart illustrates a hypothetical comparison of the total cost (initial installation plus 20 years of maintenance and potential replacements) for different siding types on a 1500 square foot home. These figures are estimations and will vary depending on location, specific materials used, and individual maintenance practices. The chart uses average costs and assumes that wood siding will require repainting every 5 years, while other siding types have minimal maintenance costs over 20 years. A replacement cost for wood siding is factored in due to the potential for more significant damage requiring section replacement over the 20-year period.
Siding Type | Initial Cost (Estimate) | Annual Maintenance (Estimate) | 20-Year Maintenance Cost | Potential Replacement Cost (20 years) | Total 20-Year Cost (Estimate) |
---|---|---|---|---|---|
Vinyl | $3000 | $50 | $1000 | $0 | $4000 |
Wood | $6000 | $300 | $6000 | $2000 | $14000 |
Fiber Cement | $7500 | $100 | $2000 | $0 | $9500 |
Metal | $10000 | $50 | $1000 | $0 | $11000 |
Note: These figures are estimations and should be considered as illustrative examples. Actual costs will vary based on several factors. It’s essential to obtain multiple quotes from contractors for accurate pricing in your specific location.
Installation Techniques for Cold Climates
Proper siding installation is crucial in cold climates to ensure both energy efficiency and structural integrity. Failing to account for the unique challenges posed by freezing temperatures and potential for ice and snow buildup can lead to costly repairs and compromised home performance. This section details best practices for installing various siding types in cold weather conditions.
Vinyl Siding Installation in Cold Climates
Vinyl siding installation in cold climates requires careful attention to detail. Expansion and contraction of the vinyl due to temperature fluctuations must be considered. Proper spacing between panels is essential to allow for this movement. Using appropriate fasteners designed for cold weather conditions is also crucial, as standard fasteners can become brittle and break in freezing temperatures. Furthermore, ensuring a good seal around windows and doors is vital to prevent air infiltration. A continuous layer of weather barrier behind the siding will add further protection against moisture intrusion. Improper installation can lead to cracking, warping, and gaps that compromise the building’s insulation.
Fiber Cement Siding Installation in Cold Climates
Fiber cement siding, while durable, also requires careful installation in cold climates. Because it is more susceptible to cracking under stress, extra care must be taken to ensure proper fastening and expansion gaps. The weight of fiber cement siding necessitates the use of robust framing and supporting structures, especially important in areas with heavy snow loads. The installation process should prioritize preventing moisture penetration, as this material is prone to damage if water seeps behind the panels. Thorough sealing of all joints and seams is critical to protect against moisture damage. Proper flashing is also crucial to divert water away from the building envelope.
Wood Siding Installation in Cold Climates
Wood siding, a classic choice, needs specific considerations for cold climates. Proper sealing and priming are essential to protect the wood from moisture damage and rot, exacerbated by freeze-thaw cycles. The wood should be acclimated to the ambient temperature before installation to minimize shrinkage and expansion issues. Using corrosion-resistant fasteners is vital, as regular fasteners may rust quickly in damp conditions. Adequate ventilation behind the siding is also crucial to prevent moisture buildup. This is particularly important in cold climates where condensation can occur more readily. Choosing wood species naturally resistant to decay and insect damage is highly recommended for longevity.
Metal Siding Installation in Cold Climates
Metal siding, known for its durability and weather resistance, requires specialized installation techniques in cold weather. The expansion and contraction of metal with temperature changes must be accounted for, with appropriate expansion gaps included during installation. The use of self-tapping screws, designed for metal and resistant to cold temperatures, is crucial. Proper flashing and sealing are critical to prevent water infiltration, especially around windows and doors. Because of the potential for wind uplift in cold, snowy conditions, extra care must be taken to secure the siding panels to the underlying structure. Using sealant specifically formulated for cold temperatures will ensure a lasting bond.
Importance of Flashing and Sealing
Proper flashing and sealing are paramount in all siding installations, particularly in cold climates. Flashing, typically made of metal, redirects water away from vulnerable areas such as window and door frames, corners, and rooflines. Sealing prevents air and water infiltration through gaps and joints. In cold climates, these measures are crucial to prevent ice dams, water damage, and mold growth. Neglecting these steps can lead to significant damage, requiring costly repairs. High-quality sealant, specifically designed for exterior applications and low temperatures, should always be used.
Challenges of Installing Siding in Freezing Temperatures
Installing siding in freezing temperatures presents several challenges. Materials can become brittle and more prone to cracking or breaking. Sealants may not adhere properly in very cold conditions. The use of heated equipment, such as heat guns, to warm materials and facilitate adhesion, is sometimes necessary but must be used carefully to avoid damage. The efficiency of the work force may also be reduced due to the difficult working conditions. Planning and preparation are key to mitigate these challenges and ensure a successful installation. Consider delaying installation until more favorable weather conditions if possible.
Maintenance and Repair of Siding in Cold Climates
Proper siding maintenance is crucial in cold climates to protect your home from damage and ensure energy efficiency. Neglecting maintenance can lead to costly repairs and reduced home value. This section details year-round care for various siding materials, focusing on challenges posed by freezing temperatures and harsh winter conditions.
Regular Inspections
Regular inspections are vital for identifying and addressing potential problems before they escalate. Ideally, conduct a thorough inspection twice a year: once in spring after the snow melts, and again in autumn before winter sets in. During these inspections, check for loose or damaged siding, cracks, gaps, and signs of moisture intrusion. Pay close attention to areas prone to water accumulation, such as corners, around windows and doors, and at ground level. Early detection allows for timely repairs, preventing minor issues from becoming major, costly problems. For example, a small crack left unaddressed can allow water to seep in, leading to wood rot or mold growth, necessitating extensive repairs.
Winter Preparation
Preparing your siding for winter’s extreme conditions is essential to prevent damage. This includes clearing away any debris, such as leaves or snow, that might accumulate against the siding. Ice dams, formed by melting snow refreezing on the roof, can cause significant damage by forcing water behind the siding. Proper roof ventilation is key to preventing ice dams. Consider installing ice and water shields under the roofing material to provide an extra layer of protection. Finally, inspect and clean gutters and downspouts to ensure proper water drainage away from the foundation and siding. Blocked gutters can lead to water overflow and potential damage.
Addressing Ice Damage
Ice damage is a common problem in cold climates. Expanding ice can cause cracking and warping of siding, particularly in areas where water has accumulated. If you notice ice forming behind the siding, it’s crucial to address the issue promptly. This may involve carefully removing the ice and addressing the underlying cause of water intrusion. In cases of significant damage, professional repair may be necessary. For example, severely cracked vinyl siding panels will likely need replacement. Repairing ice damage quickly minimizes the extent of the damage and prevents further deterioration.
Dealing with Cracking
Cracking can occur in various siding materials due to temperature fluctuations and age. Minor cracks in vinyl siding can often be repaired with caulk, ensuring a watertight seal. Larger cracks or damage may require replacing the affected panel. Wood siding is more susceptible to cracking, and repairs may involve patching or replacing damaged boards. Fiber cement siding is more durable but can still crack under extreme stress. Repairing cracks promptly prevents water penetration and maintains the structural integrity of the siding. Ignoring cracks can lead to significant water damage and costly repairs in the long run. For example, untreated cracks in wood siding can lead to rot and insect infestation.
Maintenance by Siding Type
The maintenance requirements vary depending on the siding material. Vinyl siding generally requires minimal maintenance, involving occasional cleaning with soap and water. Wood siding requires more frequent maintenance, including regular cleaning, staining, and caulking. Fiber cement siding is relatively low-maintenance but requires periodic cleaning and sealing. Metal siding is durable and requires minimal maintenance but may need occasional cleaning and repainting to maintain its appearance. Regular inspections and addressing issues promptly will prolong the lifespan of any siding material.
Repair Techniques
Repair techniques also vary by siding material. Vinyl siding repairs often involve replacing damaged panels. Wood siding repairs may involve patching, replacing boards, or applying wood filler. Fiber cement siding repairs are more complex and may require specialized tools and expertise. Metal siding repairs often involve patching or replacing damaged sections. It’s advisable to consult a professional for complex repairs to ensure proper installation and prevent further damage. Attempting complex repairs without the proper skills can lead to more extensive damage and increased repair costs.
Choosing the Best Siding for Specific Cold Climate Conditions
Selecting the ideal siding for a cold climate involves careful consideration of several factors beyond just material type. The severity and specific characteristics of the cold climate significantly impact siding performance, longevity, and energy efficiency. Understanding these nuances is crucial for making an informed decision that protects your home and reduces energy costs.
Factors Influencing Siding Selection in Cold Climates
The choice of siding material is heavily influenced by the unique challenges posed by different cold climate regions. High snowfall areas require siding that can withstand significant weight without damage, while regions with extreme temperature fluctuations demand materials that can expand and contract without cracking or warping. Wind exposure also plays a critical role, impacting the need for durable and wind-resistant siding. Furthermore, the prevalence of ice and moisture necessitates materials with excellent water resistance and resistance to ice damage.
Siding Material Recommendations Based on Climate Conditions
The optimal siding material varies depending on the specific cold climate conditions. For instance, areas experiencing heavy snowfall and high winds might benefit from the strength and durability of fiber cement siding, while regions with milder winters and less extreme temperature swings might find vinyl siding a more cost-effective option. In areas prone to significant ice buildup, metal siding’s resistance to ice damage is a considerable advantage. The following table summarizes recommendations:
Climate Condition | Recommended Siding | Reasoning |
---|---|---|
High Snowfall, High Winds | Fiber Cement | High strength, durability, and resistance to impact damage. |
Extreme Temperature Fluctuations | Metal | Excellent dimensional stability, minimal expansion and contraction. |
Moderate Snowfall, Mild Winters | Vinyl | Cost-effective, relatively low maintenance. |
Areas Prone to Ice Buildup | Metal | Resistant to ice damage and moisture penetration. |
Influence of Local Building Codes and Regulations on Siding Selection
Local building codes and regulations often dictate specific requirements for siding materials, installation methods, and fire resistance. These regulations are designed to ensure the safety and structural integrity of buildings within a particular region. For example, some areas may mandate the use of fire-resistant siding materials, particularly in areas with high wildfire risk, even if the climate is generally cold. Before selecting siding, it is crucial to consult local building codes and obtain necessary permits to ensure compliance. Failure to comply can result in fines or even necessitate costly remediation work. For example, a municipality might specify minimum wind load ratings for siding in hurricane-prone areas, even if the average winter temperature is below freezing. This ensures the siding can withstand high winds, even in cold conditions.
Concluding Remarks
Ultimately, selecting the best siding for a cold climate involves a careful balancing act between initial cost, long-term maintenance, energy efficiency, and aesthetic preferences. While each material offers unique advantages and disadvantages, understanding their properties and considering your individual circumstances will empower you to make a well-informed decision that ensures both comfort and cost savings for years to come. Remember to consult with local building professionals to ensure compliance with all relevant codes and regulations for optimal results.